The process of making cement is not as complicated as it appears. It is manufactured in an industrial setting using step-by-step procedures. Furthermore, several machines or instruments are required for the production of cement. To produce cement, you’ll need a few basic substances in addition to the tools. The cement manufacturing process will be thoroughly explored in this article, but first we must gain a thorough understanding of cement. Here are some lesser-known facts about cement, as well as a broad overview.
It is a soft, powdery, powder-like substance that is generally available in the marketplace and commonly employed in building structures. It is built entirely of natural materials such as clay, limestone, sand, or shale. Cement, when combined with water and sand, can form a solid and durable mass known as concrete. Silicon, calcium, iron, and aluminum are four important ingredients that must be combined in the right proportions to form cement. Calcium for cement production comes from limestone, which is a naturally occurring calcium supply. Silicon, on the other hand, has been taken from sand or clay, and iron and aluminum, respectively, have been removed from iron ore and bauxite. To manufacturing, these basic elements must be combined in the correct proportions.
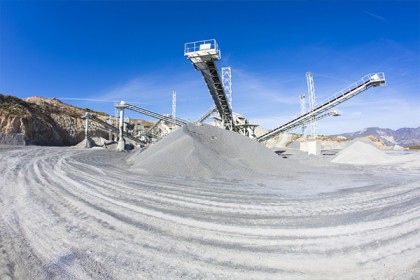
How Cement is made in Factories in India Step by Step?
In a broader sense, a 4-step process must be performed to manufacture cement. The first phase involved the production of clinker from raw materials, followed by the production of cement from the clinker. The initial phase might be entirely dry, completely wet, semi-dry, or semi-wet, depending on the state of the raw ingredients or their availability. The following are the 4 phases that must be followed in order to create cement:
Step 1: Mining
Quarrying the primary raw materials, mostly limestone, clay, and other components, is the first step in the manufacturing process.
Step 2: Crushing
After quarrying, the rock is crushed. There are several stages to this process. Initially, the rock is crushed to a maximum size of about 6 inches. In secondary crushers or hammer mills, the rock is crushed to roughly 3 inches or smaller.
Step 3: Grinding, Homogenization, and Clinkerization are all steps in the Clinkerization Process:
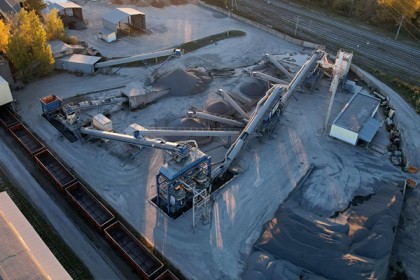
Crushed rock is blended with additional components such as iron ore or fly ash and pulverized, mixed, and supplied to a cement kiln next in the making process. A kiln is a type of oven with a thermally isolated chamber that produces temperatures high enough to finish a process such as hardening, drying, or chemical reactions.
In massive cylindrical steel rotating kilns walled with special firebrick, the cement kiln warms all of the components to over 2,700 degrees Fahrenheit. Kilns can be as large as 12 feet in diameter, large enough to fit an automobile inside, and, in many cases, longer than a 40-story structure. The axis of the huge kilns is angled slightly away from the horizontal.
The slurry of finely ground raw material is put into the upper end. A roaring explosion of flame, created by perfectly regulated burning of powdered coal, oil, alternative fuels, or gas under forced draught, can be found near the lower end. Certain elements are pushed off in the form of gases as the material travels through the kiln. The remaining elements combine to produce clinker, a new material. Clinker emerges from the kiln in the form of grey marble-sized balls.
Step 4:- Cement Grinding, Storage and Packaging
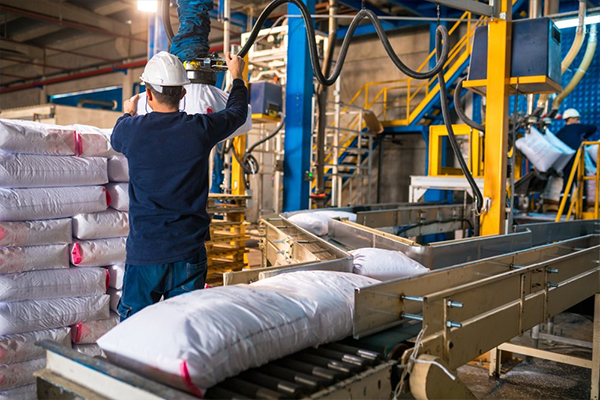
Clinker and gypsum are taken from their respective hoppers and fed to the mills for Ordinary Portland Cement (OPC), limestone for limestone cement, and slag for slag cement. In the first and second chambers of the ball mill, the feed is ground to a fine powder.
There is a set amount of ball charge in each chamber, ranging in size from 17mm to 90mm. The mill discharge is fed into a bucket elevator, which transports the material to a separator, which separates the fine and coarse material. The latter is sent into the mill, where it is reground before being stored in concrete silos.
It is taken from silos and transported to automatic electronic packers, where it is bagged in 50-kilogram bags and loaded into trucks.
You Can Also Check This Out: What is Cement Plastering? Everything You Need to Know